Service & Support
SERVICE & SUPPORTService & Support
Location Position:Home > Service & SupportShanghai Dikong Intelligent Cloud Management System
Shanghai Dikong intelligent cloud management system is widely used in intelligent lighting control system, intelligent home system, intelligent energy consumption management system, etc. It uses 4G network (mobile, linkage, telecom), Through the wireless data transfer unit (DTU), connect any DICON terminal devices or third-party devices (such as electricity meters and water meters with RS485 modbus communication protocol) distributed within the network coverage to the DICON intelligent cloud platform, and establish an independent account on the cloud platform, so that users can access the designated account anytime and anywhere through computers or mobile phones to manage the entire system.
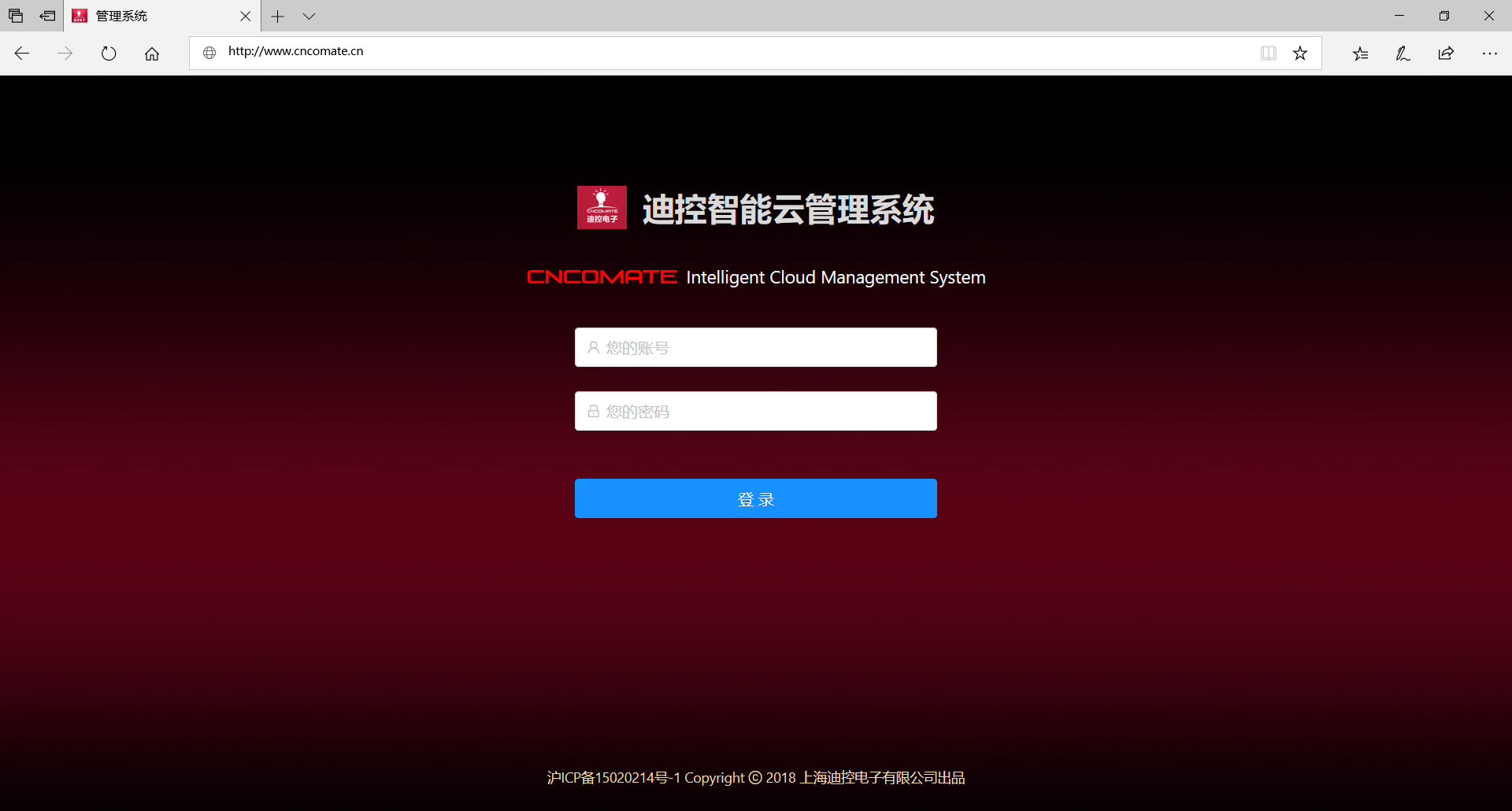
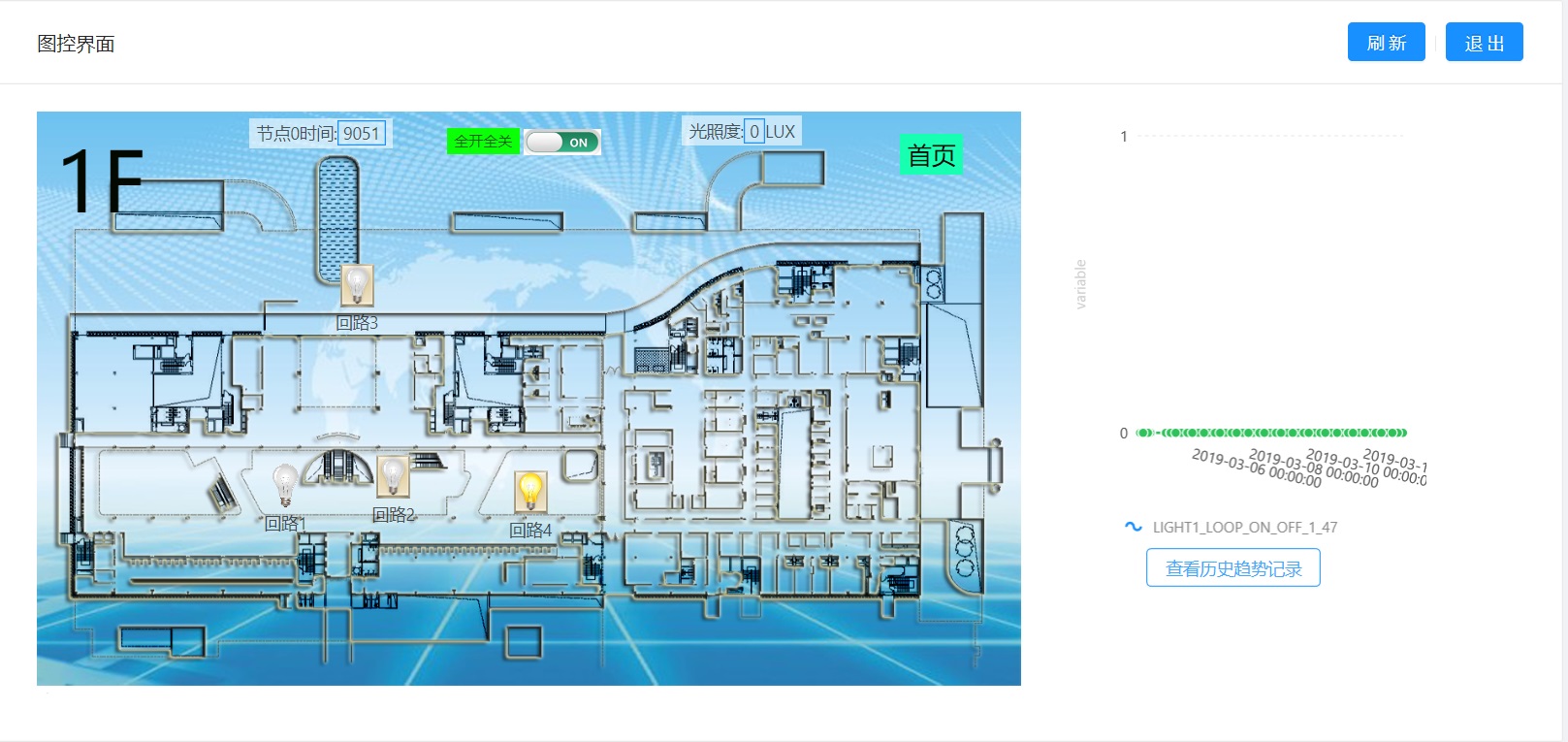
Main features:
1. Multi user and multi authority management of the system: user levels can be configured, and different user levels can be assigned with different operation permissions.
2. Perfection of system security login strategy: users can set SMS authentication login or specify a computer's MAC address for login (MAC address is burned by the computer manufacturer, and generally cannot be changed) to improve user system security.
3. Complete system functions:
1) Map control management interface: the user can insert the base map, insert the equipment to be monitored at the corresponding position on the base map, edit the name of the equipment, etc., then you can see its running status in real time and control it in real time.
2) Group setting and control function: the user can establish different groups according to the area and running time of the controlled equipment, which can be controlled manually or automatically with one key.
3) Timing control (timing) function: After the timing settings are saved, the corresponding timing parameters will be saved to the serial port device. The serial port device can perform timing logic operation according to the parameters. In this way, the cloud platform can synchronize the timing with the local timing, which can greatly improve the reliability of timing operation. There is no need to worry about the inability to control on time due to unstable signals.
4) Time sequence control can be divided into ordinary time sequence, specifying the day time sequence and the closing day. In the ordinary timing setting and the specified day timing setting, unlimited execution time nodes can be added, and timing control can meet any requirements through timing setting.
5) Abnormal alarm function: the user can select SMS alarm or email alarm. Once the equipment acts abnormally, the designated staff will be informed at the first time.
6) Historical record curve list function: after the user selects the relevant parameters, the historical data curve chart is automatically generated. According to the curve chart, the control scheme of lighting and other equipment can be reasonably optimized and configured to extend the service life of the lamps.
7) Parameter setting backup function: All the configuration parameters (such as timing, scenarios, etc.) set by the user can be backed up and exported to a personal computer or imported into the cloud system at any time.
8) Historical operation record query function: multiple user names can be configured under each project account. The system records who logs in and who has done what operations.
The super administrator will assign the user name, initial password, user operation authority level, and security login method (SMS authentication login, MAC address login, or direct password login without authentication) according to user needs.
1) Direct login without verification:
1. Dikong Company shall provide the user name and initial password required above according to user requirements.
2. Browser input URL http://www.cncomate.cn The login page is shown below:
2. Operation: http://localhost:10099/macs Obtain the MAC address of the user's local computer.
3. Send the following mac codes to the Dicontrol Hypertube, for example: ["58:8a: 5a: 3c: af: 77", "00: e1:8c: db: e6: f2", "00: e1:8c: db: e6: f1"]
4. Enter the user name and password.
5. The user will enter the project directly.
6. If the user name is not logged in on the specified computer, it will be rejected, as shown in the following figure:
3) Login by SMS authentication:
1. The user enters the user name and password.
2. Get the SMS verification code.
3. The user enters the project directly.
4. Enter the project main menu interface:
Device settings: create a DTU device, add a serial port device under the DTU device, and view the online status of the DTU device.
Variable editing: you can view the current values of variables for all devices, and modify the current values and distribute them to the field devices.
Connection status: view the online status of all serial port devices.
Group settings: create user-defined groups.
Timing setting: create user-defined timing.
Equipment monitoring: for single equipment or all equipment, all equipment and variables in the project can be selectively controlled.
File management: upload map control and project base map files, and support jpg, jpeg, png, gif, and bmp formats.
Map control management: edit the project map control operation interface to control the project visually. Contains curve chart controls. The variable curve is actually recorded.
Abnormal alarm: set the abnormal alarm activation variable, and send alarm information notification by SMS or email.
Data backup: the parameter settings of the backup project can be loaded at any time to avoid data loss caused by operational errors.
Historical data: view variable history to facilitate users to find operation records.
Diagram control operation: the diagram control interface set by the diagram control management monitors the equipment.
Chapter III System Architecture and Wiring Diagram of Equipment in Distribution Box
For more details and high-definition drawings, please consult our relevant technicians!